Aalto University - ARTS 3D Printing
Vat Polimerization (SLA)
Умови завершення
Переглянути
SLA processes is the original 3D printing technology. It use a single-point UV light source to cure liquid resin layer-by-layer. Contrary to FDM, these printers create models upside-down. The resin is set into a UV resistant covered tank, and a platform will drop into the resin, where it exposes to the laser and solidifies. With each layer, the platform will move up in the Z axis creating one layer at the time.
After printing, the part needs to be cleaned from excess resin with isopropyl alcohol, and cured with a UV light to improve its physical characteristics. The result is a smooth print with almost invisible layers and high details, ideal for final prototypes.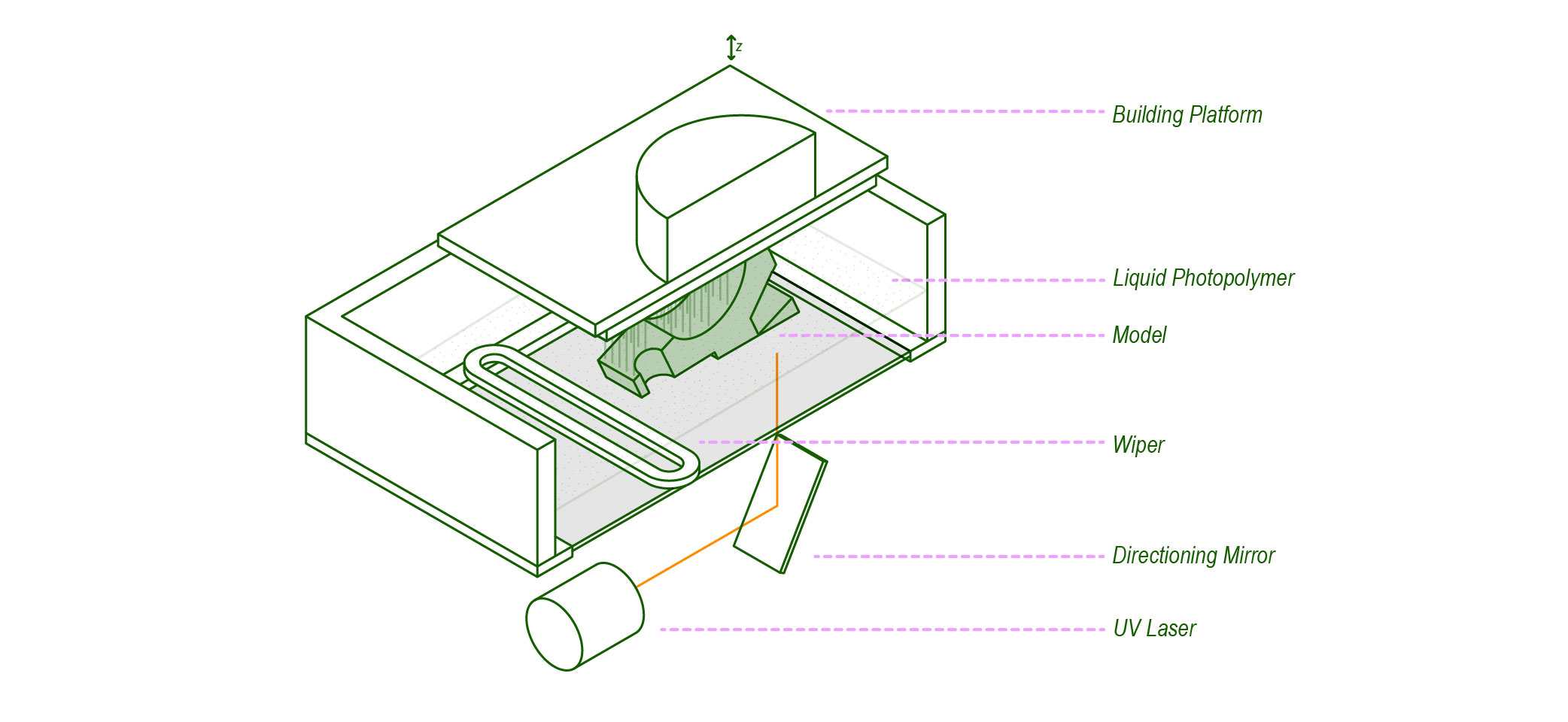
At the workshop, we have two Formlabs Form 2 SLA printers.
SLA technology can create prints that are highly accurate in dimension and detail, with a very smooth surface. That is the reason why it is very popular in the medical industry, more specifically in the manufacturing of dental parts. In the same way, there is a possibility to print in a large range of resin materials with particular properties and finishes: from white to colored resin, as well as flexible and high temperature resistant materials. The library of materials is constantly evolving, and today it is even possible to print with experimental materials such as ceramic-like resins. On the downside, printed parts tend to be quite brittle, and degrade easily when exposed to sunlight and UV light. In addition, it is always necessary to include support structures to the piece, which requires mechanical removing and some post processing in order to achieve a prototype without marksCharacteristics of SLA Prints
- Are highly detailed and accurate. The level of detail depends on the size of the curing laser, which depends on the type of machine used.
- Objects are not directly built on the printing platform; instead, they are set in an angle and require a support structure that will hold them – independently of their geometry. This support is always printed in the same material of the part, and requires to be mechanically removed after the print is done.
- Prints are completely solid. This leads to using more material, therefore, more expensive. In order to have an empty interior, the pieces need to be designed hollow. Doing this would decrease material usage and printing time, but also presents other challenges in the design.
- Printers can only use one material at a time. In order to have multi-material parts, they need to be printed separately, and assembled afterwards.
Materials
- Standard: It comes in four finishes: white, black, grey and clear. The first three ones are opaque. The clear resin can be used for any parts requiring translucency. In order to get a transparency, it requires to be postprocessed by manually sanding and polishing the part. More about that HERE (external link)
If you want to learn more about other materials click HERE (external link)
Остання зміна: понеділок 6 липня 2020 12:17 PM